Toyotas Kanban-System wurde als Antwort auf die Herausforderungen der ineffizienten Produktion und der unkontrollierten Lagerhaltung entwickelt. Doch schnell wurde es weit mehr als nur eine Methode zur Bestandsverwaltung – es revolutionierte das Workflow-Management und bildet heute das Fundament des Lean Manufacturing.
In diesem umfassenden Leitfaden werden wir die Entwicklung von Kanban bei Toyota nachverfolgen, seine praktischen Wurzeln und die Kernprinzipien untersuchen. Außerdem erfahren Sie, warum dieses System weit über die Automobilindustrie hinaus Anwendung findet und wie Unternehmen es nutzen, um Effizienz, Flexibilität und Transparenz in ihren Arbeitsprozessen zu steigern.
Indem wir die Ursprünge von Kanban verstehen, erkennen wir, wie dieses adaptive System es ermöglicht, Ressourcen, Aufgaben und Zeit optimal zu verwalten. Vom klassischen Toyota-Kanban bis zur digitalen Anwendung in modernen Unternehmen – dieser Leitfaden bietet Ihnen praxisnahe Einblicke und wertvolle Informationen.
In diesem Artikel
Was ist Kanban?
Kanban ist ein visuelles System zur Steuerung von Arbeitsabläufen, das ursprünglich von Toyota entwickelt wurde. Es ermöglicht Unternehmen, Prozesse effizienter zu gestalten, Verschwendung zu minimieren und die Produktivität zu steigern. Durch eine klare Visualisierung der Arbeitsschritte hilft Kanban Teams, Engpässe frühzeitig zu erkennen, den Arbeitsfortschritt zu begrenzen und Prozesse kontinuierlich zu optimieren. Ursprünglich in der Fertigungsindustrie etabliert, hat sich Kanban heute in vielen Bereichen bewährt, darunter Softwareentwicklung, Gesundheitswesen und Finanzdienstleistungen. Das bei Toyota entwickelte ist ein visuelles System, das hilft, Verschwendung zu minimieren und die Produktivität zu steigern. Teams verwenden es, um Aufgaben zu überwachen, den Arbeitsfortschritt zu begrenzen und Prozesse zu optimieren. Es ist anpassungsfähig und wird in der Fertigung, in der Softwarebranche, im Gesundheitswesen und anderen Bereichen eingesetzt.
Die wichtigsten Elemente von Kanban
Kanban-Karten
- Jede Kanban-Karte repräsentiert eine Aufgabe oder ein Arbeitselement.
- Sie können physisch (Papierkarten) oder digital (Software-gestützt) sein.
- In der Toyota-Produktion signalisieren Kanban-Karten, wann neue Teile benötigt werden, um einen kontinuierlichen Materialfluss zu gewährleisten.
Kanban Board
- Ein visuelles Werkzeug zur Organisation von Aufgaben über verschiedene Phasen hinweg.
- Typische Spalten sind "Zu erledigen", "In Bearbeitung" und "Erledigt".
- Toyota nutzte Kanban-Boards, um Verzögerungen zu vermeiden und Mitarbeitern Klarheit über anstehende Aufgaben zu geben.
Die sechs Regeln von Kanban
- Visualisieren des Workflows - Kanban-Boards und -Karten machen den Arbeitsprozess sichtbar.
- Work In Progress (WIP) begrenzen - Begrenzt die Anzahl gleichzeitiger Aufgaben, um Engpässe zu vermeiden.
- Fokus auf den Fluss - Sicherstellt, dass Aufgaben reibungslos und effizient durch das System laufen.
- Prozessrichtlinien klar formulieren - Definiert klare Abläufe für ein besseres Verständnis.
- Feedback-Schleifen einrichten - Regelmäßige Überprüfung und Anpassung zur kontinuierlichen Verbesserung.
- Gemeinsam verbessern, experimentell weiterentwickeln - Fördert eine Kultur der ständigen Optimierung basierend auf Daten und Erfahrungswerten.
Warum ist Kanban seffektiv?
Kanban optimiert Arbeitsabläufe, indem es Transparenz schafft und Teams hilft, sich auf wertschöpfende Aufgaben zu konzentrieren. Durch die Begrenzung laufender Arbeiten und eine kontinuierliche Anpassung der Prozesse wird eine hohe Effizienz erreicht. Toyota konnte mit diesem System seine Lagerbestände drastisch reduzieren und Engpässe vermeiden – ein Erfolg, der Kanban zu einem zentralen Bestandteil des Lean Managements gemacht hat.
Wie erfand Toyota Kanban?
Kanban entstand aus der Inspiration von Taiichi Ohno, einem leitenden Ingenieur bei Toyota, der die effiziente Bestandsverwaltung in Supermärkten beobachtete. Dort wurden Produkte basierend auf der tatsächlichen Nachfrage nachgefüllt, anstatt große Vorräte vorzuhalten. Ohnübertrug dieses Prinzip auf die Produktion und entwickelte ein System, das den Materialfluss steuert und Verschwendung minimiert.
Die Herausforderungen in den 1940er Jahren
In den 1940er Jahren kämpfte Toyota mit Produktionsproblemen:
- Teile wurden zu früh oder zu spät geliefert, was zu überfüllten Lagern oder Produktionsverzögerungen führte.
- Das Push-basierte System führte zu Überproduktion und hohen Lagerhaltungskosten.
- Fehlende Synchronisation zwischen den Fertigungsstationen sorgte für Ineffizienzen.
Einführung des Pull-Systems mit Kanban
Ohnerkannte, dass die Lösung in einem flexiblen, nachfragegesteuerten System lag. Das Kanban-System führte einen visuellen Prozess ein, bei dem jede Produktionsstufe nur dann neue Materialien anforderte, wenn sie wirklich benötigt wurden. Dieses "Pull-System" ersetzte die traditionelle Push-Methode und führte zu folgenden Verbesserungen:
- Reduktion von Überbeständen: Teile wurden erst bestellt, wenn sie benötigt wurden.
- Höhere Produktionseffizienz: Engpässe wurden minimiert und die Produktionszeit verkürzt.
- Bessere Qualitätskontrolle: Fehler wurden frühzeitig erkannt und behoben.
Die Rolle der Kanban-Karten
Die zentrale Komponente des Systems war die Kanban-Karte:
- Sie signalisierte den Bedarf an neuen Teilen in einer bestimmten Produktionsstufe.
- Nach der Verwendung eines Teils wurde die Karte zurückgeschickt, um den Nachschub zu initiieren.
- Sblieb der Materialfluss konstant und Lagerbestände wurden auf ein Minimum reduziert.
Das Kanban-Board als Steuerungselement
Neben den Kanban-Karten führte Toyota Kanban-Boards ein, um den Produktionsprozess zu visualisieren:
- Arbeitsschritte wurden in Spalten wie "Zu erledigen", "In Bearbeitung" und "Fertiggestellt" eingeteilt.
- Engpässe wurden sofort sichtbar und konnten behoben werden.
- Die Transparenz des Workflows ermöglichte eine kontinuierliche Optimierung.
Warum war Kanban für Toyota ein Erfolg?
Die Implementierung von Kanban war ein entscheidender Wendepunkt für Toyota:
- Lagerbestände wurden um bis zu 75 % reduziert.
- Produktionszeiten wurden gestrafft und Ausschuss minimiert.
- Das System wurde flexibel und konnte sich an Marktschwankungen anpassen.
Durch die Einführung von Kanban konnte Toyota seine Produktion revolutionieren. Die Kombination aus visuellen Werkzeugen, Echtzeit-Nachschubsteuerung und kontinuierlicher Verbesserung machte das Kanban-System zu einem der zentralen Bestandteile des Toyota Produktionssystems (TPS). Heute wird Kanban weit über die Automobilbranche hinaus eingesetzt und hat sich als eine der effektivsten Methoden des Lean Managements etabliert.
Vergleich von Kanban mit anderen Lean-Prinzipien
Kanban ist ein zentrales Element des Toyota Produktionssystems (TPS), aber es funktioniert nicht isoliert. Es wird oft mit anderen Lean-Methoden kombiniert, um die Effizienz weiter zu steigern. Besonders bedeutend sind 5S und Poka-Yoke, die sich nahtlos in das Kanban-System integrieren lassen.
5S: Die Grundlage für eine strukturierte Produktionsumgebung
5S ist eine Methode zur Arbeitsplatzorganisation, die dazu beiträgt, dass Kanban effizienter eingesetzt wird. Die fünf Prinzipien sind:
- Sortieren (Seiri) - Unnötige Gegenstände werden entfernt, um den Arbeitsplatz effizient zu gestalten.
- Systematisieren (Seiton) - Werkzeuge und Materialien werden sangeordnet, dass sie leicht zugänglich sind.
- Säubern (Seiso) - Regelmäßige Reinigung verhindert Fehler und Defekte.
- Standardisieren (Seiketsu) - Einheitliche Prozesse gewährleisten eine gleichbleibende Qualität.
- Selbstdisziplin (Shitsuke) - Mitarbeiter werden darauf trainiert, die 5S-Regeln dauerhaft einzuhalten.
Durch die Anwendung von 5S bleibt die Arbeitsumgebung organisiert, wodurch das visuelle Kanban-System noch effektiver wird.
Poka-Yoke: Fehlervermeidung durch smarte Prozesse
Poka-Yoke ist eine Technik zur Fehlervermeidung, die sicherstellt, dass Produkte oder Prozesse möglichst fehlerfrei ablaufen. Im Kontext von Kanban bedeutet dies:
- • Automatische Erkennung von Engpässen: Durch Kanban-Boards können potenzielle Probleme frühzeitig sichtbar gemacht werden.
- • Visuelle Hinweise: Farbmarkierungen oder Sensoren können anzeigen, ob Materialien korrekt verwendet wurden.
- • Qualitätskontrolle in Echtzeit: Poka-Yoke-Techniken ermöglichen es, fehlerhafte Teile sofort auszusortieren und den Produktionsfluss nicht zu stören.
Synergien zwischen Kanban, 5S und Poka-Yoke
Diese Methoden ergänzen sich gegenseitig:
- • 5S sorgt für eine aufgeräumte Umgebung, die für ein reibungsloses Kanban-System notwendig ist.
- • Kanban schafft Transparenz über den Arbeitsfluss und gibt visuelle Hinweise, wo Optimierungen notwendig sind.
- • Poka-Yoke stellt sicher, dass Fehler minimiert werden, sodass die Kanban-Prozesse effizienter laufen.
Kanban ist ein mächtiges Werkzeug zur Steuerung von Produktions- und Geschäftsprozessen, aber seine volle Wirksamkeit entfaltet sich erst in Kombination mit anderen Lean-Methoden wie 5S und Poka-Yoke. Unternehmen, die diese Prinzipien gemeinsam anwenden, profitieren von höherer Effizienz, reduzierten Fehlern und einer optimierten Produktion.
Wie hat sich Kanban seither bei Toyota bewährt und verbreitet?
Die Einführung von Kanban bei Toyota war ein revolutionärer, aber nicht reibungsloser Prozess. Anfangs stand das Unternehmen vor der Herausforderung, das optimale Gleichgewicht zwischen Produktionskapazität und Lagerbeständen zu finden. Durch die konsequente Nutzung von Echtzeitdaten und die enge Zusammenarbeit mit Zulieferern konnte Toyota das System jedoch schrittweise optimieren.
Toyota band seine gesamte Lieferkette in das Kanban-System ein, wodurch es gelang, Engpässe zu reduzieren, den Materialfluss zu verbessern und die Effizienz der Produktion zu steigern. Kanban wurde zu einem zentralen Bestandteil des Toyota Produktionssystems (TPS) und legte den Grundstein für das moderne Lean Manufacturing.
Wie hat Kanban Toyota geholfen?
Kanban ermöglichte Toyota eine radikale Umstellung auf ein nachfragegesteuertes Pull-System, das bedeutende Produktionshürden beseitigte:
- Reduktion der Lagerkosten: Produktionsphasen forderten Teile nur an, wenn sie wirklich benötigt wurden.
- Effizienzsteigerung: Durch eine verbesserte Steuerung der Materialflüsse wurden Überbestände und Verschwendung eliminiert.
- Kürzere Produktionszeiten: Die kontinuierliche Anpassung des Workflows verhinderte Verzögerungen und Engpässe.
Dank dieser Optimierungen konnte Toyota innerhalb von drei Jahren die Lagerbestände um 75 % reduzieren und die Fehlmengen um 95 % verringern. Zudem erleichterte der visuelle Arbeitsprozess es den Teams, Engpässe schnell zu identifizieren und zu beseitigen, ohne die Produktqualität zu gefährden.
Globale Verbreitung von Kanban
Die bahnbrechenden Erfolge bei Toyota sorgten dafür, dass Kanban weltweit Aufmerksamkeit erregte. Schon in den 1970er Jahren übernahmen zahlreiche Unternehmen aus der Fertigungsindustrie ähnliche Systeme, um ihre Lieferketten zu optimieren und Verschwendung zu reduzieren. In den folgenden Jahrzehnten fand Kanban Anwendung in immer mehr Branchen:
- Softwareentwicklung: In den 2000er Jahren begannen IT-Teams, Kanban-Boards für das agile Projektmanagement zu nutzen. Das einfache Spaltenprinzip ("Zu erledigen", "In Bearbeitung", "Erledigt") erleichterte die visuelle Steuerung von Aufgaben.
- Gesundheitswesen: Kliniken und Krankenhäuser setzen Kanban zur Verwaltung von Patientenströmen und Behandlungspriorisierungen ein.
- Einzelhandel: Durch Kanban-gesteuerte Bestandsverfolgung konnten Unternehmen ihre Lager effizienter verwalten und Engpässe vermeiden.
Das Wachstum von Kanban und technologische Integration
Der Erfolg von Kanban liegt in seiner Fähigkeit, sich an neue Technologien und Anforderungen anzupassen. Digitale Kanban-Tools ermöglichen heute eine automatisierte Prozesssteuerung, die in Echtzeit auf veränderte Bedingungen reagieren kann. Dies macht Kanban zu einem zentralen Bestandteil von agilen Methoden und kontinuierlicher Verbesserung.
Beispiele für moderne Anwendungen von Kanban:
- KI-gestützte Kanban-Systeme helfen Unternehmen, datenbasierte Entscheidungen zu treffen und Engpässe vorherzusagen.
- IoT-Integration ermöglicht eine automatisierte Materialanforderung basierend auf Sensor- und Produktionsdaten.
- Cloud-Plattformen bringen Kanban-Boards in remote arbeitende Teams, wodurch die Zusammenarbeit globaler Unternehmen erleichtert wird.
Kanban vs. Scrum – Ein kurzer Überblick
Scrum ist eine weitere weit verbreitete agile Methode, die oft mit Kanban verglichen wird. Während Kanban einen kontinuierlichen Fluss von Aufgaben ermöglicht, arbeitet Scrum mit festen Iterationen (Sprints). Einige zentrale Unterschiede:
- Zyklus vs. Fluss: Scrum organisiert die Arbeit in wiederkehrende Sprints (z. B. zwei Wochen), während Kanban einen fortlaufenden Prozess ohne festgelegte Zeitabschnitte nutzt.
- Rollenverteilung: Scrum definiert spezifische Rollen wie Scrum Master, Product Owner und Entwicklungsteam. Kanban hat keine vordefinierten Rollen.
- Flexibilität: Kanban eignet sich besonders für sich ständig ändernde Anforderungen, während Scrum durch feste Sprint-Ziele strukturierter ist.
Die fortwährende Bedeutung von Kanban
Moderne Unternehmen benötigen Werkzeuge, die sowohl Effizienz als auch Anpassungsfähigkeit sicherstellen – Kanban erfüllt genau diese Anforderungen. Es hebt sich vom traditionellen Projektmanagement ab, da es Teams ermöglicht, sich spontan an neue Anforderungen anzupassen.
Die Flexibilität von Kanban ist besonders wertvoll für Unternehmen in volatilen Märkten oder für Organisationen, die auf kontinuierliche Innovation setzen. Durch Echtzeit-Feedback und klare Visualisierung von Prozessen hilft Kanban, die Transparenz zu erhöhen, Überlastungen zu reduzieren und Arbeitsabläufe effizient zu optimieren.
Von den Ursprüngen von Kanban bei Toyota bis hin zu seinen modernen digitalen Anwendungen bleibt das System ein bewährtes Modell für das Management von Veränderungen. Die Kombination aus Workflow-Optimierung, datenbasierten Entscheidungen und kontinuierlicher Verbesserung macht Kanban zu einem unverzichtbaren Werkzeug in der heutigen Geschäftswelt.
Beste Kanban Tools
Während Haftnotizen für einfache Aufgaben geeignet sind, erfordern komplexe Workflows digitale Tools zur Umsetzung von Kanban. Kanban-Software bietet Boards, angepasste Workflows, Zusammenarbeit, Dateneinblicke und mehr. Nach meinem gründlichen Test sind hier die besten Optionen.
EdrawMind
Mit EdrawMind vereinen sich Mind Mapping und Kanban in einer einzigen Oberfläche. Damit können Sie Aufgaben einfach verwalten und Ideen visuell organisieren. Sie können Boards erstellen, den Fortschritt verfolgen und Ihren Workflow anpassen.
Funktionen und Vorteile
- Visuelles Workflow-Management: Visualisieren Sie Ihre Aufgaben mit den übersichtlichen, einfachen Boards von EdrawMind und behalten Sie sden Überblick.
- Planen leicht gemacht: Verwenden Sie Mind Maps, um Ideen zu sammeln, und übertragen Sie diese dann in ein Kanban-Board, um Aufgaben einfach zu verwalten.
- Benutzerfreundlichkeit: Die intuitive Oberfläche hilft Ihnen, den Status von Aufgaben zu beurteilen und Probleme im Workflow mühelos zu erkennen.
- Anpassungsfähigkeit: Sie können Ihre Kanban-Boards individuell gestalten, indem Sie die Farben anpassen und Daten, Spalten und Beschriftungen ändern.
- Plattformübergreifende Kompatibilität: Greifen Sie von jedem Gerät aus auf Ihre Kanban-Boards zu und machen Sie das Aufgabenmanagement einfach und effizient.
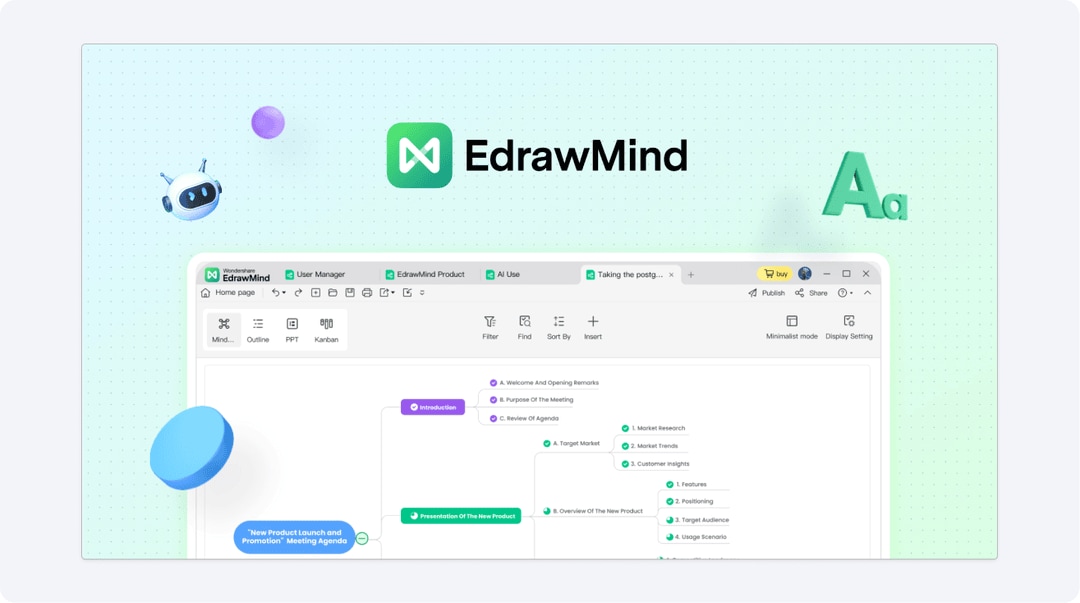
Kanban Tool
Das Kanban-Tool verwendet visuelle Boards, um die Aufgabenverwaltung übersichtlich und effizient zu gestalten. Sie verschieben die Karten zwischen den Phasen, während Sie vorankommen, mit einer minimalistischen Oberfläche, die die Ablenkung gering hält. Anpassbare Funktionen wie Farben und Spalten sorgen für zusätzliche Flexibilität.
Funktionen und Vorteile
- Visuelles Workflow-Management: Dank des visuellen Layouts können Sie den Fortschritt leicht verfolgen und Workflow-Probleme schnell erkennen.
- Zusammenarbeit: Die Zusammenarbeit wird einfach, da mehrere Benutzer direkt mit den Boards interagieren können.
- Analysen und Berichte: Erhalten Sie wertvolle Daten zur Workflow-Leistung und zu Engpässen.
- Integrationen: Integrieren Sie Apps wie Google Calendar oder Dropbox, um alles an einem Ort zu haben.
- Zeiterfassung: Mit der Zeiterfassungsfunktion können Sie die Dauer von Aufgaben messen, was Ihnen beim Projektmanagement helfen kann.
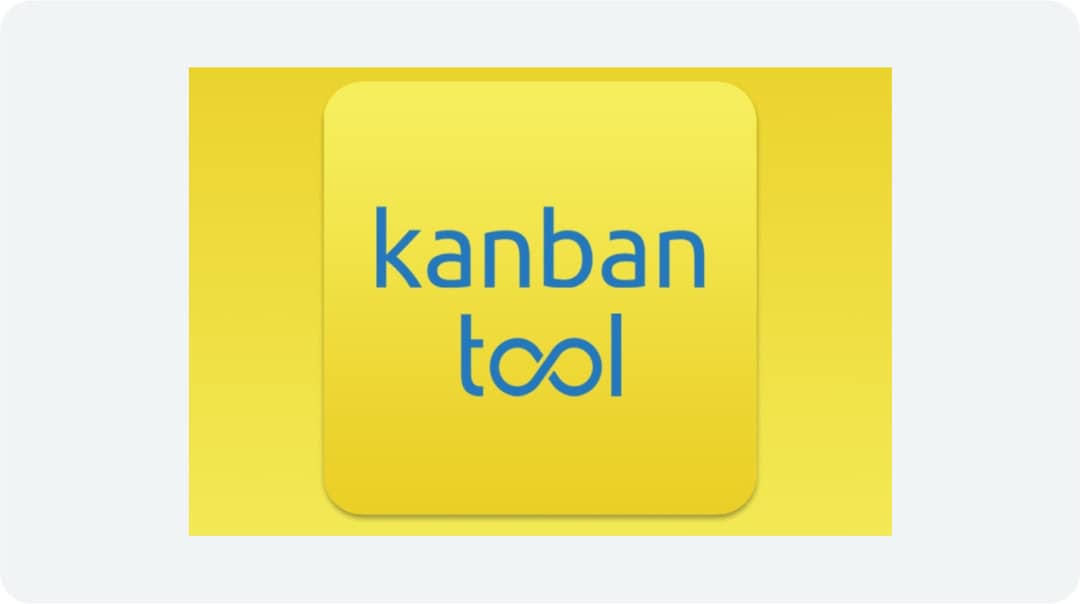
KanbanFlow
KanbanFlow ist ein cloudbasiertes Tool, mit dem Sie Aufgaben effizient verwalten können. Es ist ganz einfach, Boards einzurichten und Aufgaben als Karten hinzuzufügen. Die Karten können zugewiesen, mit Fristen versehen und zur besseren Organisation beschriftet werden.
Funktionen und Vorteile
- Die Schwimmbahnen unterteilen die Aufgaben in Zeilen für verschiedene Teams oder Projekte und vereinfachen sdie Verwaltung des Workflows.
- Mit der Zeiterfassungsfunktion können Sie sehen, wie viel Zeit jede Aufgabe in Anspruch nimmt. Es hilft dabei, Engpässe zu erkennen und zukünftige Arbeiten abzuschätzen.
- Der Pomodoro-Timer unterteilt die Arbeit in kurze Intervalle mit Pausen und verbessert sdie Konzentration und Arbeitseffizienz.
- Dank der Funktionen für die Zusammenarbeit können Teams mit Sofortbenachrichtigungen und gemeinsamen Boards auf dem Laufenden bleiben.
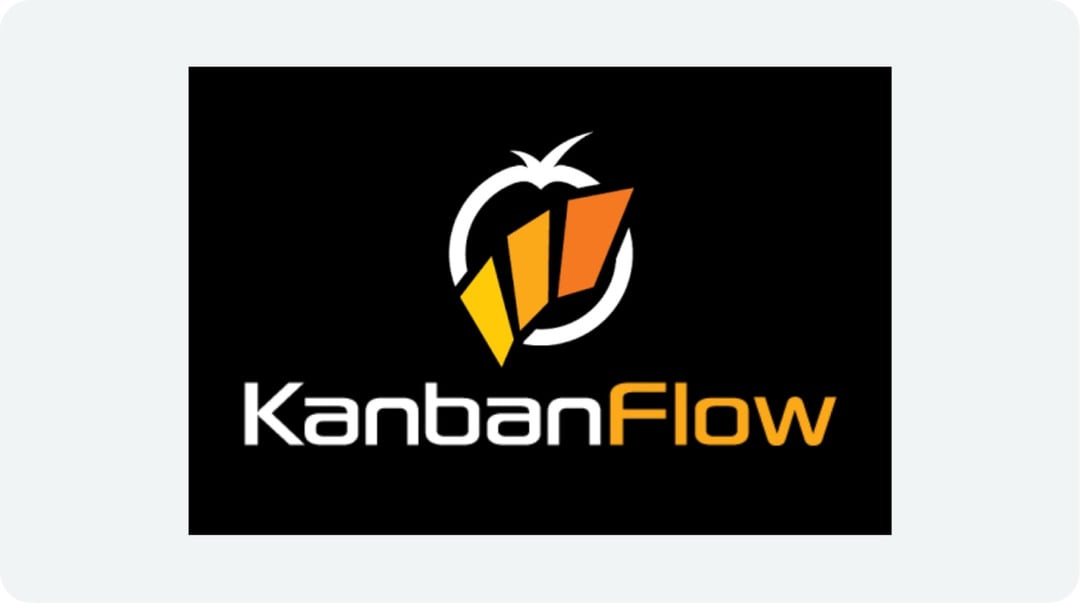
Fazit
Die Entwicklung von Kanban von Toyotas Produktionslinie zu einem globalen Workflow unterstreicht seinen bleibenden Wert. Ursprünglich zur Minimierung von Verschwendung und Verbesserung der Effizienz entwickelt, haben sich seine Grundprinzipien mittlerweile in verschiedensten Industrien bewährt.
Kanban erleichtert nicht nur die Verwaltung von Aufgaben, sondern fördert auch klare Kommunikation, eine transparente Arbeitsweise und kontinuierliche Verbesserung. Es geht über das einfache Organisieren von Arbeit hinaus und bietet eine Strategie zur Optimierung von Arbeitsprozessen und Reduzierung von Engpässen.
Mit dem Wachstum der Industrien und der verstärkten Einführung digitaler Technologien wird Kanban immer relevanter. Die Integration von KI, Big Data und Automatisierung wird das System weiter verbessern und Unternehmen noch mehr Flexibilität und Effizienz bieten. Trotz aller Innovationen bleibt jedoch eines konstant: Die Prinzipien von Kanban sind ein zeitloses Werkzeug für Prozessoptimierung und schlankes Management.
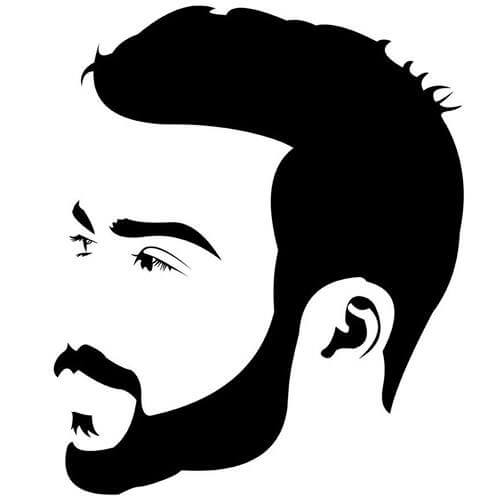